Advanced Welding WPS: Tailoring Requirements for Complex Projects
The Ultimate Overview to Welding WPS Procedures: A Comprehensive Review for Welders
In the elaborate world of welding, Welding Procedure Specs (WPS) serve as the backbone of ensuring high quality, consistency, and security in welding procedures (welding WPS). As we dig right into the various elements of a WPS and explore the intricacies of certification and certification, we will uncover the vital duty these procedures play in the world of welding.
Relevance of WPS Procedures
Recognizing the importance of Welding Procedure Requirements (WPS) treatments is crucial for ensuring the high quality and stability of bonded frameworks. WPS procedures work as a roadmap for welders, outlining the essential actions, criteria, and products required to achieve a sound weld. By adhering to WPS standards, welders can ensure consistency in their job, resulting in dependable and structurally sound welds.
Among the primary reasons WPS procedures are vital is their role in preserving weld top quality and stability. Complying with the defined welding criteria and methods outlined in the WPS assists avoid flaws such as porosity, breaking, or insufficient fusion, which can compromise the toughness and durability of the weld. Additionally, WPS treatments are crucial for ensuring compliance with sector standards and codes. By following well-known WPS guidelines, welders can demonstrate that their work satisfies the needed demands for safety and security and high quality, offering guarantee to customers, examiners, and regulatory bodies. Fundamentally, the value of WPS procedures can not be overstated, as they are fundamental to attaining regular, top quality welds that meet sector criteria and specs.
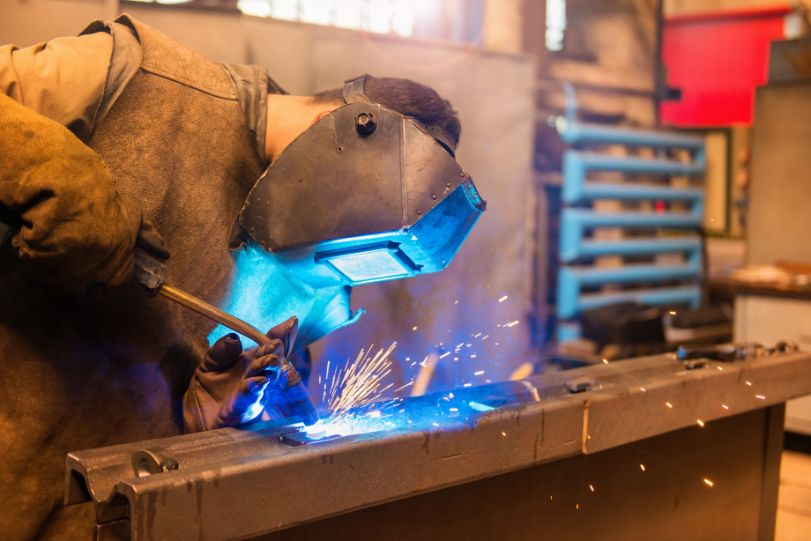
Elements of a WPS
A Welding Procedure Spec (WPS) usually comprises important parts that detail the particular demands for carrying out a weld, guaranteeing uniformity and quality in the welding process. The vital parts of a WPS consist of crucial variables such as base steels, filler metals, interpass and preheat temperature levels, welding procedures, protecting gases, welding settings, and post-weld warm therapy demands.
Base metals refer to the products being joined, while filler steels are utilized to load the void between the base metals throughout welding. Preheat and interpass temperature levels are essential for managing the warm input and protecting against concerns like splitting or distortion. The welding procedure outlines the specific strategy to be utilized, whether it's gas metal arc welding (GMAW), secured metal arc welding (SMAW), or an additional method. Securing gases protect the weld swimming pool from climatic contamination. Welding settings specify the orientations in which welding can be carried out. Post-weld warmth treatment might be necessary to eliminate tensions and boost the weld's homes. A thorough understanding of these elements is critical for producing a efficient and thorough WPS.

Certification and Qualification
Having actually established the necessary parts of a Welding Procedure Specification (WPS), the focus now shifts towards the vital facets of credentials and qualification in welding practices.
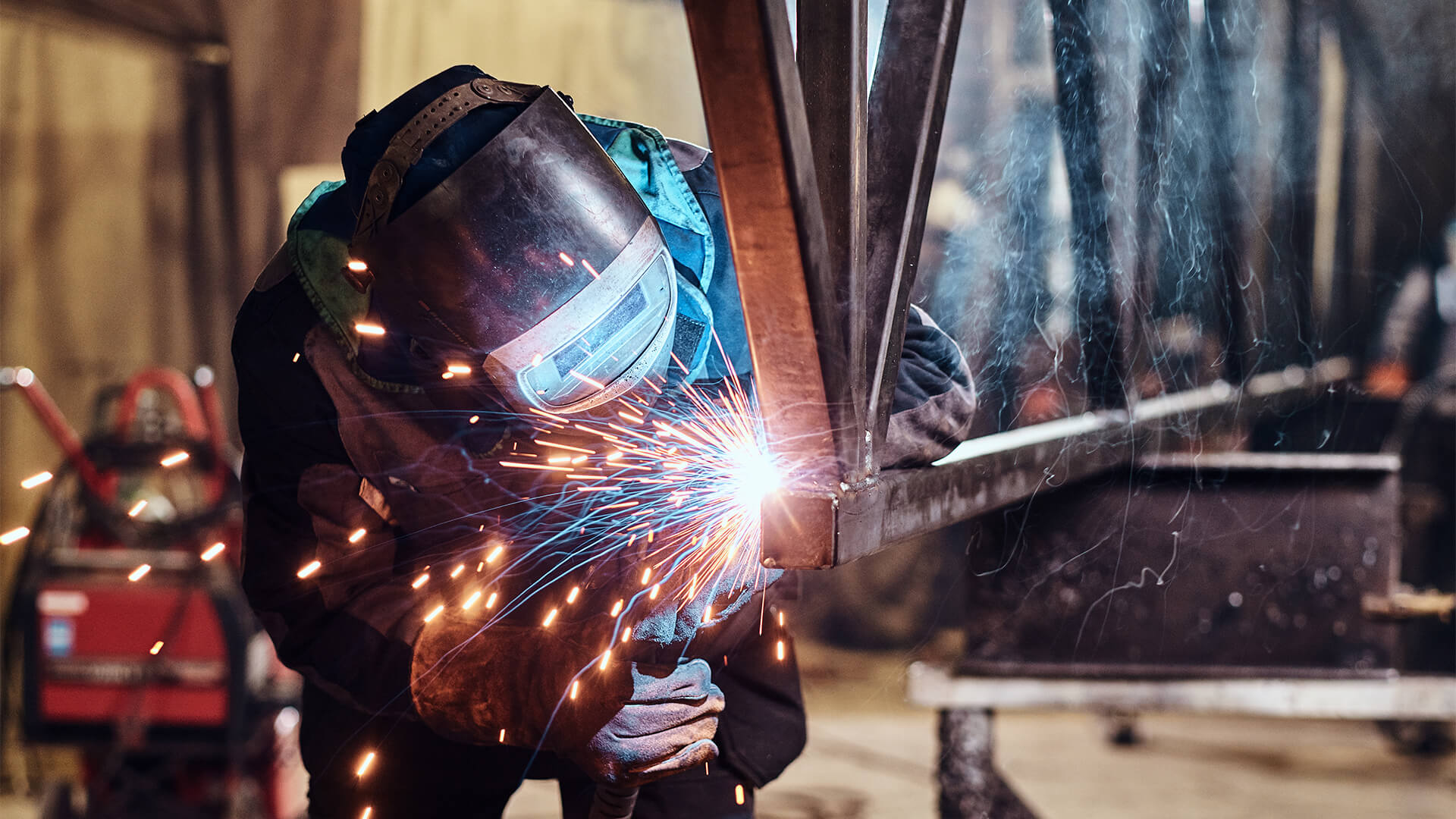
Qualification, on the other hand, is the official acknowledgment of a welder's qualifications by a pertinent certification body or organization. Welding qualifications are generally based on the particular welding procedures, products, and settings a welder is qualified to function with. Holding a legitimate welding accreditation shows that a welder meets market criteria and is proficient to perform welding tasks to the needed requirements.
Creating a WPS
To establish a Welding Treatment Requirements (WPS) that satisfies industry standards, cautious factor to consider of welding processes, materials, and operational specifications is essential (welding WPS). The primary step in developing a WPS is to determine the welding procedure to be utilized, such as gas steel arc welding (GMAW) or protected metal arc welding (SMAW) Once the welding procedure is established, the following crucial aspect is picking read the appropriate materials, thinking about variables like base metal kind, density, and joint style. Functional criteria such as welding existing, voltage, traveling rate, and shielding gas composition must additionally be meticulously defined in the WPS.

Applying and Keeping Track Of WPS
Upon completing informative post the detailed Welding Treatment Requirements (WPS) that diligently details welding processes, products, functional parameters, and high quality assurance actions, the emphasis shifts to successfully executing and keeping track of the well-known procedures. Implementation involves making sure that all welders included in the task know with the WPS and follow it thoroughly throughout the welding process. This requires providing adequate training and guidance to ensure adherence to the specified procedures. Checking the WPS involves continual oversight to verify that welding tasks line up with the recorded specifications. Inspections, screening, and quality assurance procedures are vital elements of the monitoring procedure to determine any type of deviations or problems without delay. Routine audits and evaluations of the welding procedures assist in maintaining uniformity and high quality throughout the project. Reliable application and monitoring of the WPS are critical for making sure the stability, toughness, and safety of the welded joints, eventually adding to the total success of the welding job.
Final Thought
To conclude, understanding and adhering to Welding Treatment Requirements (WPS) is vital for welders to ensure high quality, uniformity, and safety and security in their work. By recognizing the parts of a WPS, obtaining proper certifications and qualifications, creating comprehensive treatments, and applying and checking them effectively, welders can enhance their skills and efficiency in welding techniques. Sticking to WPS procedures is important for creating top notch welds and conference sector criteria.
In the intricate world of welding, Welding Procedure Requirements (WPS) offer as the foundation of making look at this now certain quality, consistency, and safety in welding procedures. The welding procedure outlines the specific strategy to be made use of, whether it's gas steel arc welding (GMAW), secured steel arc welding (SMAW), or an additional technique.To develop a Welding Procedure Requirements (WPS) that meets market requirements, cautious consideration of welding processes, materials, and operational criteria is essential. The first action in developing a WPS is to recognize the welding procedure to be used, such as gas metal arc welding (GMAW) or shielded steel arc welding (SMAW)Upon settling the detailed Welding Procedure Specification (WPS) that thoroughly information welding processes, materials, functional parameters, and top quality guarantee actions, the emphasis changes to properly carrying out and keeping an eye on the well established procedures.